How to Integrate a Wrap Around Labeler into an Existing Production Line
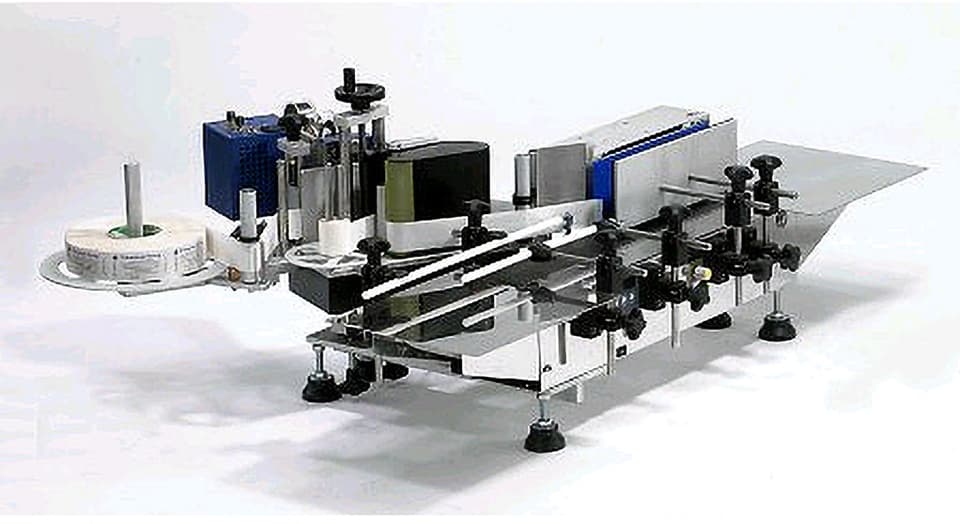
Fitting a new piece of machinery into an existing hectic production line may sound a challenging task, particularly where an important process such as labeling is concerned. Nevertheless, when planned appropriately, the concept of introducing a wrap around labeler into an already installed composition may prove very successful, allowing to be more efficient, accurate in labeling, and, overall, able to produce more items. When labelling your bottles, jars or cans, this is how to successfully introduce a wrap around labeler into your production line whilst not having to disrupt your work flow.
Analyze Your Output Process
Considering investing in a wrap around labeler, you ought to consider evaluating your current line. Develop a flow map of the whole process including the filling, capping of the products, pack, pallet. Tell me in what direction labelling logically fits in that stream. It is usually placed preferably after the product has been sealed and prior to the secondary packaging. With knowledge of how fast your system can run at, and its capacity, you can select a labeler that will fit your needs and possibly push you beyond what you previously accomplished.
Select a Matching Labeler
Not every wrap around labeler is a creation of the same mould. Determine how fast your line is, how large your containers are and the mounting space. Your selected wrap around labeler must be able not only to deal with your kinds of containers but must also be of the speed of your current machines. Choose a labeler which will be easily adapted to the various dimensions of the products to be labeled and supports integration such as having variable speed motors and be able to be synchronized with other devices.
Make Sure The Compatibility of Conveyor System
The handoff between the conveyor system to the labeler should be smooth so that there is no interruption in the system. Make sure that your current conveyor speed, width and height may be compatible with the wrap around labeler. Most of the contemporary labelers are customizable or adjustable to fit the current arrangements. In case such is required, one can include guide rails or buffer areas to ensure that products are well oriented prior to passing the model labeling station.
Electrical and Control Integration
It will help to get the entire labeling fully automated by incorporating the wrap around labeler to your current control system. This has the capability of synchronising with the upstream and downstream machine producing a less likelihood to have misaligned labels or production jams. Plan to use sensors and programmable logic controllers (PLCs) to manage timing, stop/start sequence and to detect errors. There are also remote monitoring and diagnostics on some of the high-end labelers to gain more control.
Check and Tune up the System
Exercise the integrated system prior to production. Conduct a few batches to make sure that the accuracy of label placement and the speed synchronization and the free flow of products are achieved. Manipulate sensors, guides and the pressure of application. An excellent wrap around labeler will produce the facility of fine-tuning to perfect and reduce the wastage of labels. Make sure you provide training to operators and maintenance workers so that they can address adjustment and trouble shooting.
Regular Inspection And Support Should Be Maintained
Even after proper integration, do not forget regular inspections as a way of monitoring performance. Inspect label rolls, application heads, and alignments systems to ensure there is no wearing out. By ensuring that your wrap around labeler is in good condition, you will be ensured of a good output as well as have reduced wasted time. The provision of technical support and maintenance services (preventive) by many manufacturers might be useful to ensure smooth running of your operation.
Conclusion
Adding a wrap around labeler to the existing production line does not have to be so difficult. Given due planning, the needed hardware, with proper alignment to your existing workflow, you can get an improved accuracy of labeling, improved efficiency of operations. When done correctly, this integration will help automate your packaging operation, increase work output, enhance the success of your manufacturing facility in the long-term.